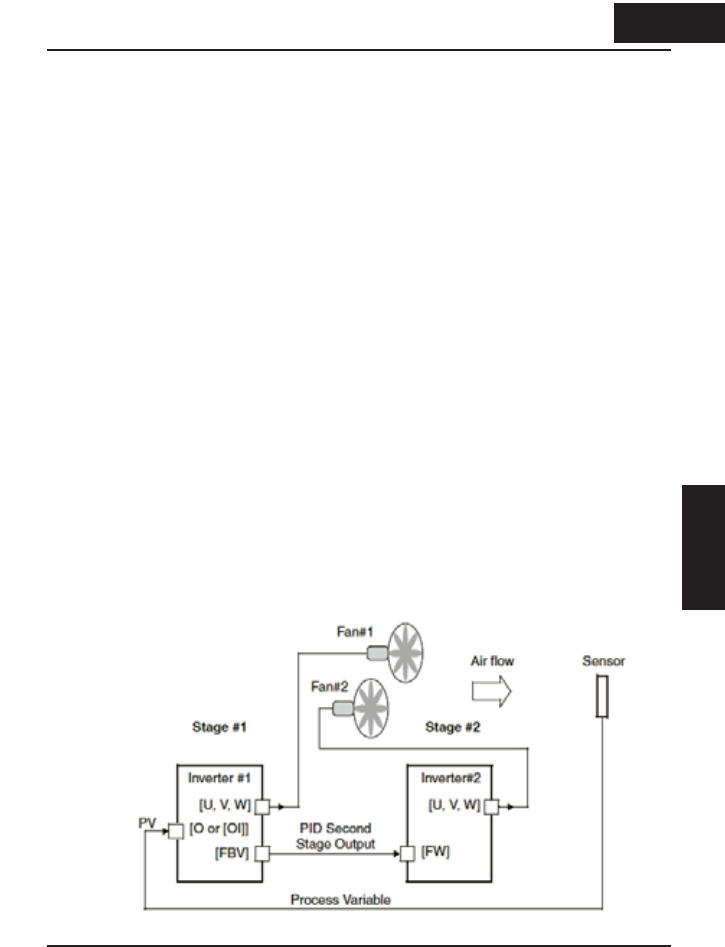
PID Second Stage Output
The inverter has a built-in PID loop feature for
two-stage control,
useful for certain
applications such as building ventilation or heating and cooling (HVAC). In an ideal
control environment, a single PID loop controller (stage) would be adequate. However,
in certain conditions, the maximum output energy from the first stage is not enough to
maintain the Process Variable (PV) at or near the Setpoint (SP). And, the output of the
first stage is in saturation. A simple solution is to add a second stage, which puts an
additional and constant amount of energy into the system under control. When size
properly, the boost from the second stage brings the PV toward the desired range,
allowing the first stage PID control to return to its linear range of operation.
The two-stage method of control has some advantages for particular applications.
x The second stage is only ON in adverse conditions, so there is an energy savings
during normal conditions.
x Since the second stage is simple ON/OFF control, it is less expensive to add than just
duplicating the first stage.
x At powerup, the boost provided by the second stage helps the process variable reach
the desired setpoint sooner than it would if the first stage acted alone.
x Even though the second stage is simple ON/OFF control, when it is an inverter you
can still adjust the output frequency to vary the boost it provides.
Refer to the example diagram below. Its two stages of control are defined as follows:
x Stage 1 - Inverter #1 operating in PID loop mode, with motor driving a fan
x Stage 2 - Inverter #2 operating as an ON/OFF controller, with motor driving a fan
Stage #1 provides the ventilation needs in a building most of the time. On some days,
there is a change in the building’s air volume because large warehouse doors are open.
In that situation, Stage #1 alone cannot maintain the desired air flow (PV sags under
SP). Inverter #1 senses the low PV and its PID Second Stage Output at [FBV] terminal
turns ON. This gives a Run FWD command to Inverter #2 to provide the additional air
flow.
447
Operations and
Monitoring
4 47
Operations and
Monitoring