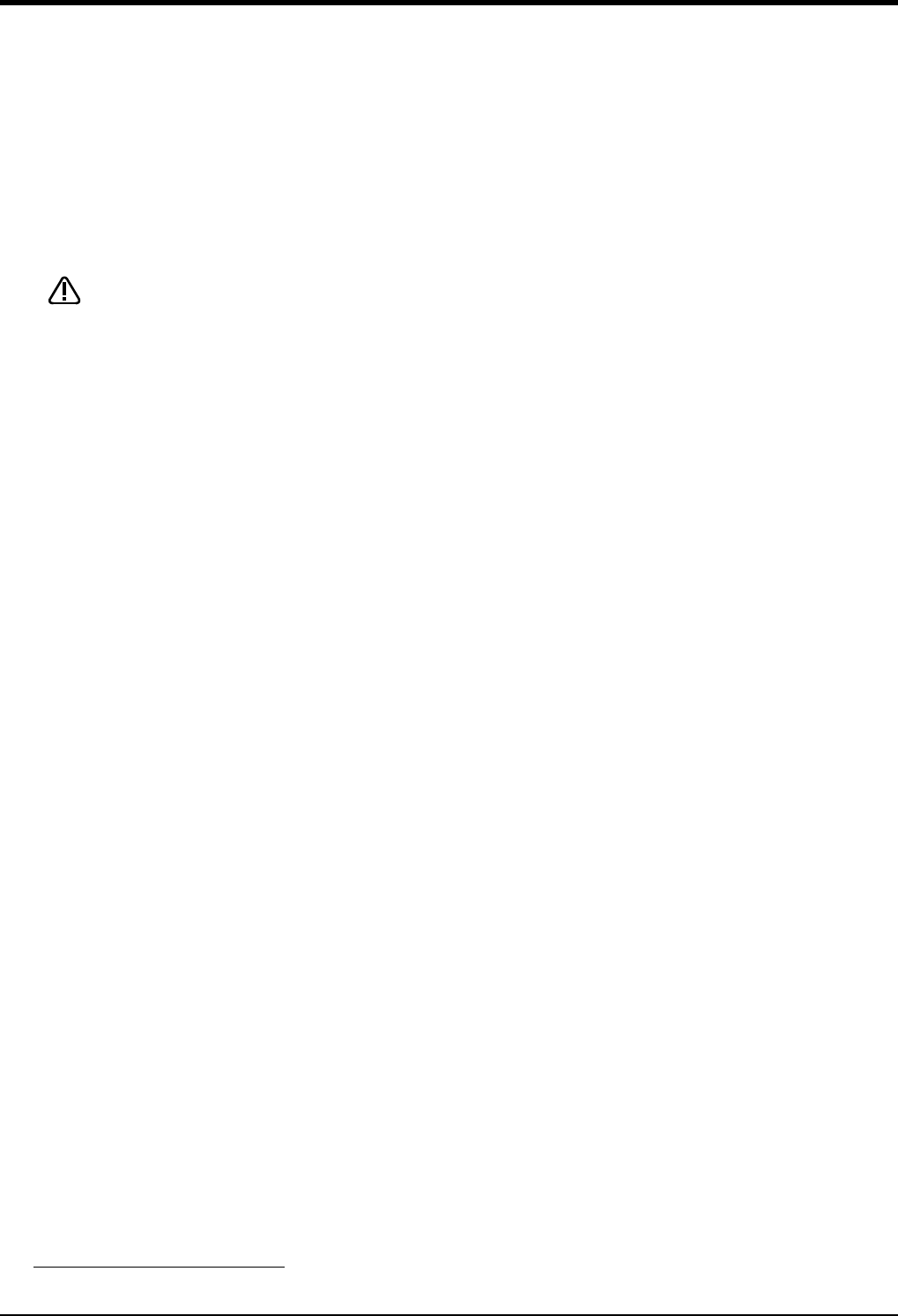
6Safety
Working environment
6-152
6.2 Working environment
Avoid installation in the following places as the equipment's life and operation will be affected by the ambient
environment conditions. When using in the following conditions, the customer must pay special attention to the
preventive measures.
(1) Power supply
・ Where the voltage fluctuation will exceed the input voltage range.
・ Where a momentary power failure exceeding 20ms may occur.
・ Where the power capacity cannot be sufficiently secured.
Please use the controller with an input power supply voltage fluctuation rate of 10% or
less. In the case of 200 VAC input, for example, if the controller is used with 180 VAC
during the day and 220 VAC during the night, turn the servo off once and then on again.
If this is not performed, an excessive regeneration error may occur.
(2) Noise
・ Where a surge voltage exceeding 1000V, 1μs may be applied on the primary voltage. Near large inverters, high
output frequency oscillator, large contactors and welding machines. Static noise may enter the lines when this
product is used near radios or televisions. Keep the robot away from these items.
(3) Temperature and humidity
・ Where the atmospheric temperature exceeds 40 degree , lower than 0 degree.
・ Where the relative humidity exceeds 85%, lower than 45%, and where dew may condense.
・ Where the robot will be subject to direct sunlight or near heat generating sources such as heaters.
(4) Vibration
・ Where excessive vibration or impact may be applied. (Use in an environment of 34m/s
2
or less during transpor-
tation and 5m/s
2
or less during operation.)
(5) Installation environment
・ Where strong electric fields or magnetic fields are generated.
・ Where the installation surface is rough. (Avoid installing the robot on a bumpy or inclined floor.)
・ Where there is heavy powder dust and oil mist present.
6.3 Precautions for handling
(1) This robot has brakes on J3 axes. The precision of the robot may drop, looseness may occur and the reduction
gears may be damaged if the robot is moved with force with the brakes applied.
(2) Avoid moving the robot arm by hand. When unavoidable, gradually move the arm. If moved suddenly, the accu
-
racy may drop due to an excessive backlash, or the backed up data may be destroyed.
(3) Note that depending on the posture, even when within the movement range, the shaft section could interfere
with the base section. Take care to prevent interference during jog.
*1)
(4) The robot arm consists of precision parts such as bearing. Lubricants such as grease are also applied on the
moving parts to keep the mechanical accuracy. In a cold start under low temperature or in the first start after
being stored for one month or longer, lubricants may not be spread enough. Such condition may lower the posi
-
tioning accuracy, cause servo and overload alarms, and early wearing of the moving parts. To avoid such situ-
ation, perform warm-up operation of the machine at a low speed (at about 20% of normal operation speed).
Move the robot arm from the lower to the upper limit of the movable range with the 30 degree joint angle or
more for about 10 minutes. After that, speed up the operation gradually.
Please use the warm-up operation. (About the details of the warm-up operation, refer to "INSTRUCTION
MANUAL/Detailed explanations of functions and operations".)
(5) When the air hoses and cables are used inside the shaft (J3 axis), the grease for cable protection may ooze out
or abrasion powders may be generated from the tip of the shaft while the robot is moving. However, move
-
ments and performance of the robot are not affected. Wipe off the grease or powders as required.
*1) Jog operation refers to operating the robot manually using the teaching pendant.
CAUTION