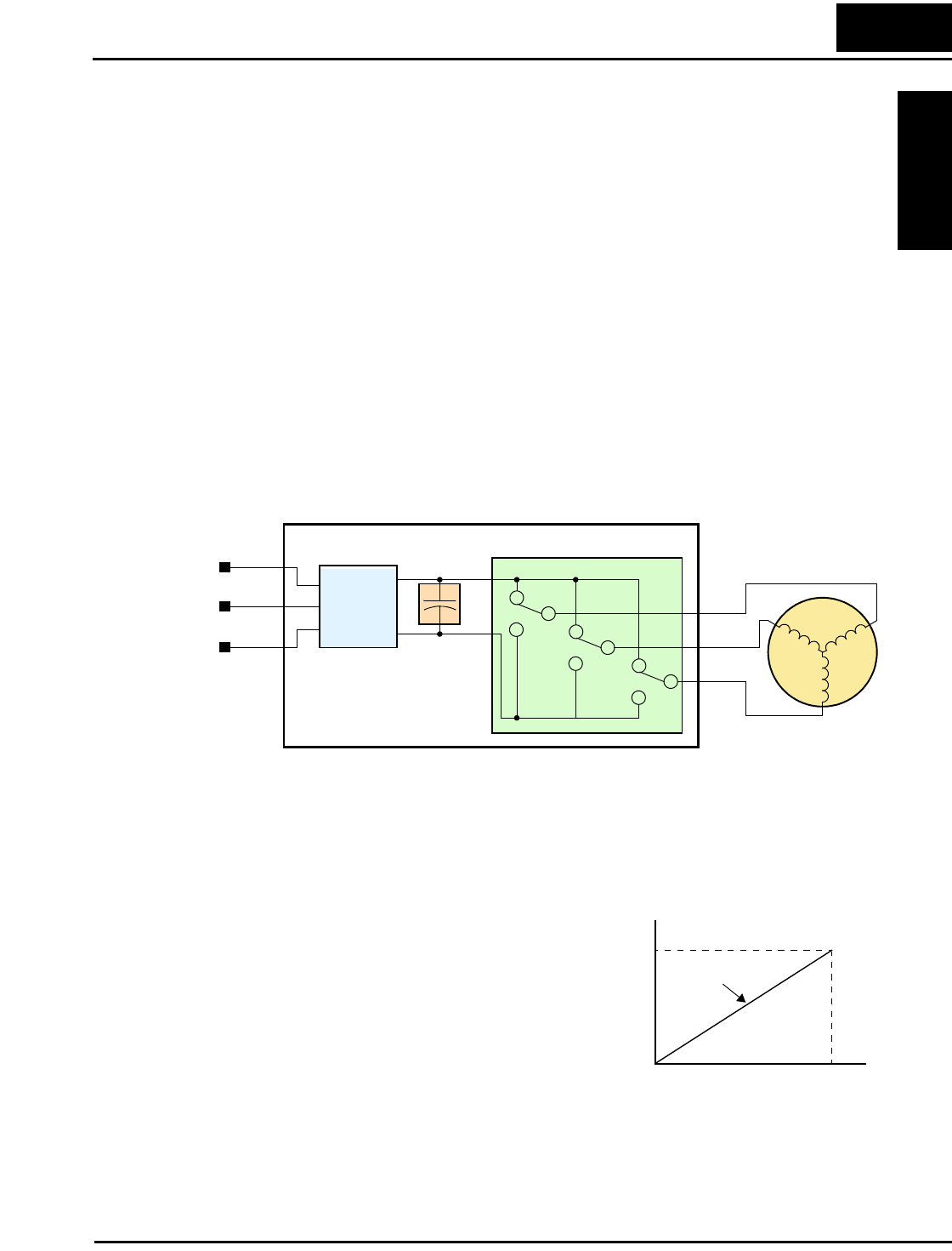
SJ300 Inverter
Getting Started
1–13
Introduction to Variable-Frequency Drives
The Purpose of
Motor Speed
Control for
Industry
Hitachi inverters provide accurate speed control for 3-phase AC induction motors. You connect
AC power to the inverter, and connect the inverter to the motor. Many applications can benefit
from the use of variable-speed drives in several ways:
• Energy savings - HVAC
• Need to coordinate speed with an adjacent process - textiles and printing presses
• Need to control acceleration and deceleration (torque)
• Sensitive loads - elevators, food processing, pharmaceuticals
What is an
Inverter?
The term inverter and variable-frequency drive are related and somewhat interchangeable. An
electronic drive for an AC motor controls the motor’s speed by varying the frequency of the
power sent to the motor.
An inverter, in general, is a device that converts DC power to AC power. The figure below
shows how the variable-frequency drive employs an internal inverter. The drive first converts
incoming AC power to DC through a rectifier bridge, creating an internal DC bus voltage. Then
the inverter circuit converts the DC back to AC again to power the motor. The special inverter
can vary its output frequency and voltage according to the desired motor speed.
The simplified drawing of the inverter shows three double-throw switches. In Hitachi inverters,
the switches are actually IGBTs (isolated gate bipolar transistors). Using a commutation
algorithm, the microprocessor in the drive switches the IGBTs ON and OFF at a very high
speed to create the desired output waveforms. The inductance of the motor windings helps
smooth out the pulses.
Torque and
Constant Volts/
Hertz Operation
In the past, AC variable speed drives used an
open loop (scalar) technique to control speed.
The constant-volts-per-hertz operation
maintains a constant ratio between the applied
voltage and the applied frequency. With these
conditions, AC induction motors inherently
delivered constant torque across the operating
speed range. For some applications, this scalar
technique was adequate.
Today, with the advent of sophisticated micro-
processors and digital signal processors
(DSPs), it is possible to control the speed and
torque of AC induction motors with unprece-
dented accuracy. The SJ300 utilizes these devices to perform complex mathematical calcula-
tions required to achieve superior performance. The technique is referred to as sensorless
vector control. It allows the drive to continuously monitor its output voltage and current, and
their relationship to each other. From this it mathematically calculates two vector currents. One
Power
Input
Inverter
L1/R
Motor
L2/S
L3/T
Rectifier
Variable-frequency Drive
Internal DC Bus
+
+
–
U/T1
V/T2
W/T3
Converter
Output frequency
Output
voltage
100%
V
0
100%
f
Constant torque