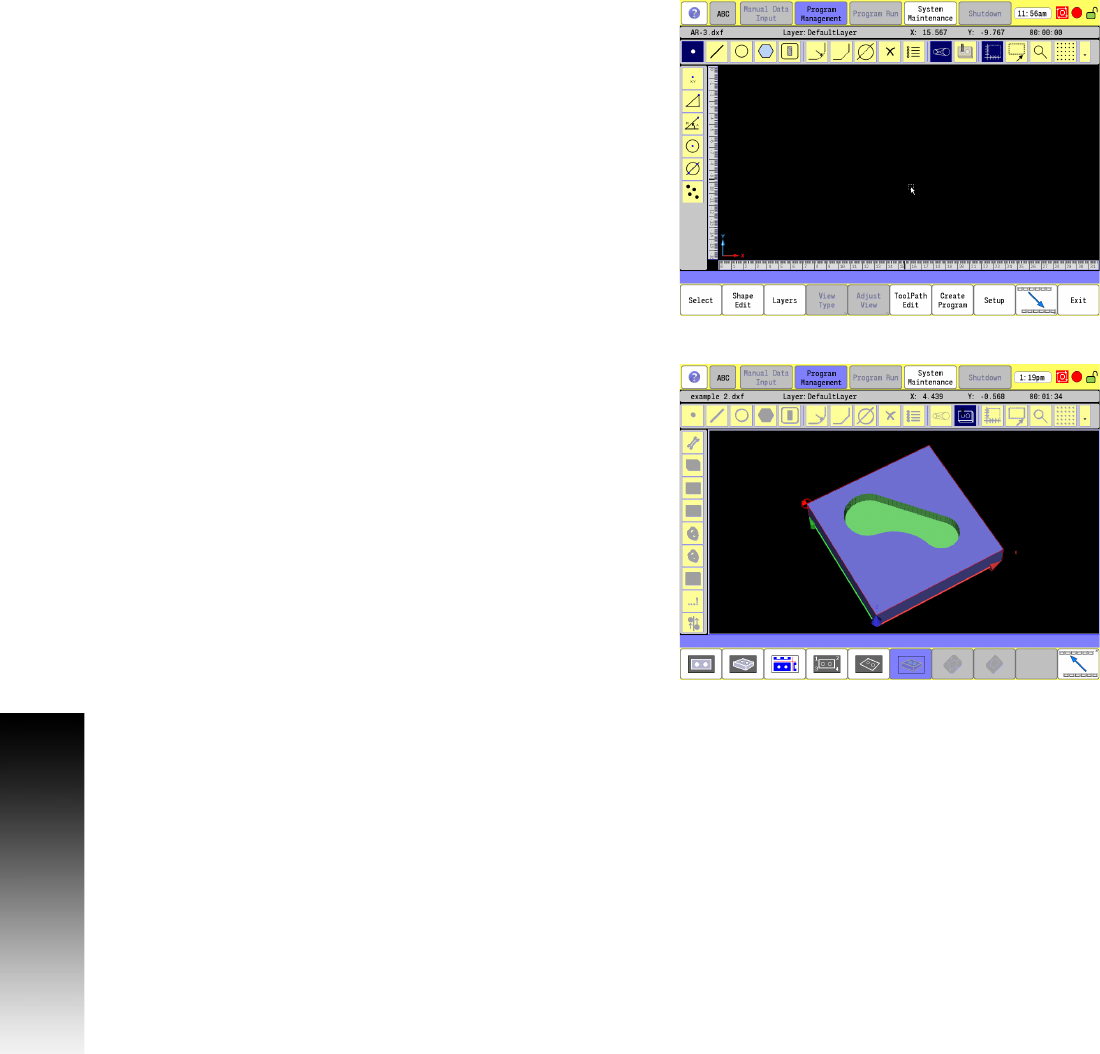
276 10 CAM: Programming
10.1 CAM Programming
10.1 CAM Programming
CAM Mode
CAM Mode is different from the standard CNC programming method
of part programming. With CAM programming, you create part
programs with the help of geometry tool buttons. These buttons
prompt you for necessary information. CAM Programming utilizes a
graphical interface and features that eliminate the need for CNC
programming and complicated calculations.
To use CAM programming, you must know the XYZ (Cartesian)
coordinate system, the polar coordinate system, and machining
sequences. Refer to chapter "2.1 Fundamentals of Positioning on
page 26”. You must make a machining plan, decide which type of
tools to use and when to use those tools in the program.
CAM programming is used to generate tool paths from “Shapes.”
These Shapes are generated from geometry created with the CAM
geometry tools, importing geometry in a DXF file or a combination
of creating and importing.
To create the geometric elements required for a part program, such
as: points, lines and circles, select the appropriate Geometry Tools
button. Next select on the appropriate sub-tool button. The CAM
software prompts you to enter the required information to create
the geometry. These entries combined with selecting shapes and
creating tool paths enable the system to perform the desired
machine sequences. As you program points, lines and circles, they
are displayed on the Graphics screen. The resulting tool path is also
shown in the graphics screen for tool path verification.
CAM mode features a powerful tool table which can be used to
calculate feeds and speeds used in the program.
To utilize this feature tools must be set up in the CAM tool table.
Feeds and speeds can also be manually entered and calculated
values overridden.
CAM Mode enables you to generate complete part programs. CAM
generated programs are based on canned cycles which makes the
program easier to edit outside of CAM if needed.