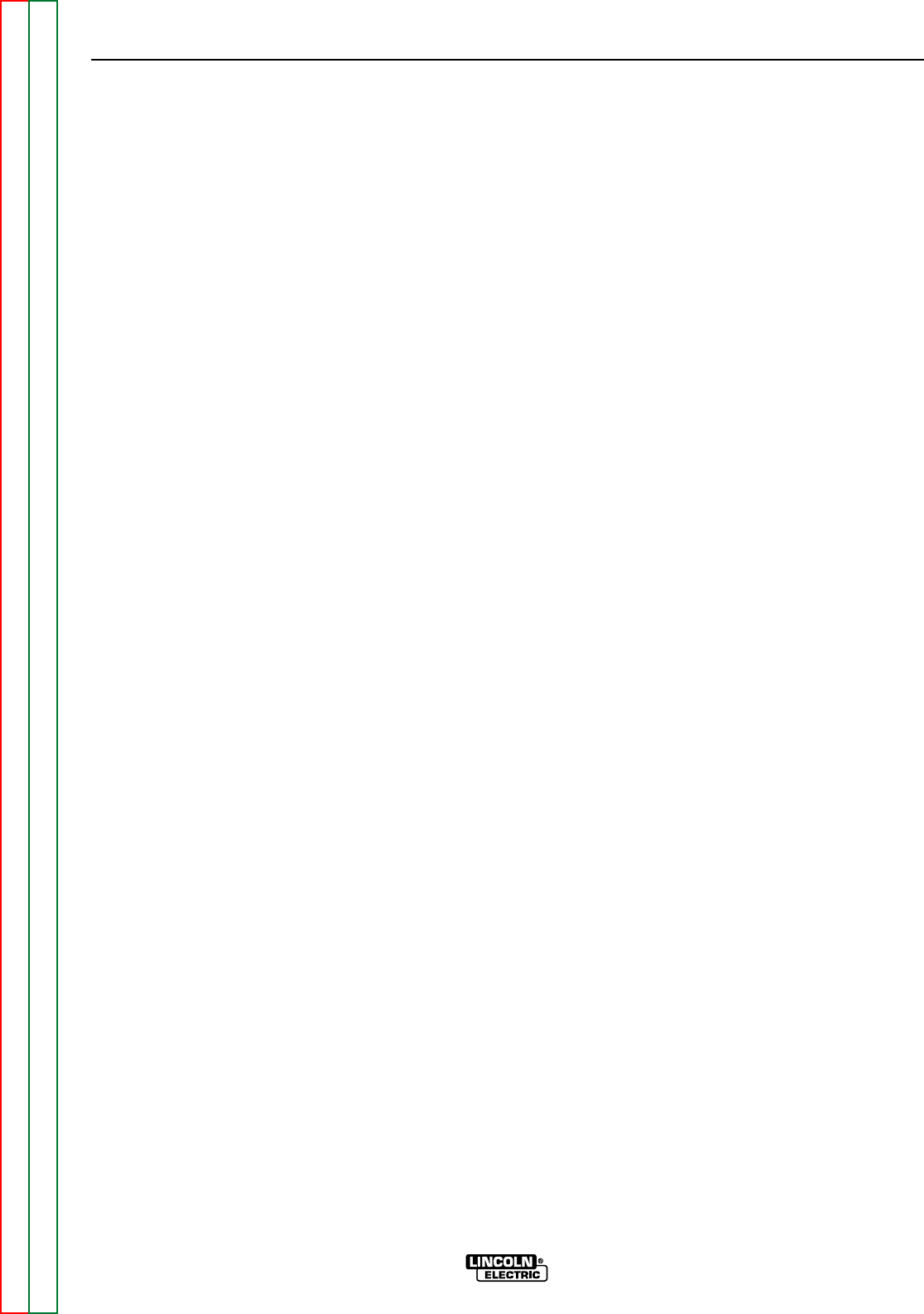
AUXILIARY POWER CONTROLS
(Figure B.1 Items 15 - 19 )
15.
120/240VAC RECEPTACLE: This is a 120/240VAC
(14-50R) receptacle that provides 240VAC or can
be split for 120VAC single phase auxiliary power.
The receptacle has a 50 amp rating. Refer to
“Auxiliary Power Receptacles” in the
Installation section for further information about
this receptacle. Also refer to “Auxiliary Power
Operation” later in this section.
16. 50 AMP CIRCUIT BREAKERS: These circuit
breaker provide separate overload current protec-
tion for each 120V circuit at the 240V receptacle.
17. 120VAC RECEPTACLES: These two 120VAC (5-
15R) receptacles with GFCI protection provide
120VAC for auxiliary power. The receptacles have
a 20 amp total rating. Refer to “Auxiliary Power
Receptacles” in the Installation section for fur-
ther information about these receptacles. Also
refer to “Auxiliary Power Operation” later in this
section.
18. 15 AMP CIRCUIT BREAKERS: These circuit
breakers provide separate overload current pro-
tection for each 120V receptacle.
19. GROUND STUD: Provides a point for connecting
the machine case to earth ground for the safest
grounding procedure. Refer to “Machine
Grounding” in the Installation section for proper
machine grounding information.
WIRE FEEDER MODE CONTROLS
(Figure B.1 Items 20 - 24 Stick & Wire model only)
20. WELD OUTPUT TERMINAL - WIRE: This 1/2-13
stud with flange nut provides a welding connection
point for the electrode or work cables. For positive
polarity welding, the electrode cable connects to
the “+” terminal and the work cable connects to the
“-” terminal. For negative polarity welding, the work
cable connects to the “+” terminal and the elec-
trode cable connects to the “-” terminal.
21. 15 AMP CIRCUIT BREAKER: This circuit breaker
provides overload protection for the 14-pin con-
nector.
22. VOLTMETER +/- SWITCH: Changes the polarity
display on the wire feeder.
23. VOLTS-AMPS SWITCH: Switches the display
between volts and amps.
24. 14 - PIN CONNECTOR: For quick connection of
wire feeder control cable.
ENGINE OPERATION
STARTING THE ENGINE
1. Open the engine compartment door and check that
the fuel shutoff valve located to the left of the fuel fil-
ter housing is in the open position (lever in line with
the hose).
2. Check for proper oil level on the oil dipstick. Close
engine compartment door.
3. Remove all plugs connected to the AC power recep-
tacles.
4. Set the IDLER switch to “AUTO.”
5. Set the RUN/STOP switch to “RUN.” Observe that
all engine protection lights momentarily turn on.
Some lights may turn off before starting. Check the
fuel gauge to make sure that there is an adequate
fuel level.
6. Press and hold the engine START button for a min-
imum of 2 seconds.
7. Release the engine START button when the engine
starts.
8. Check that the indicator lights are off. If the LOW
FUEL light is on , the engine will shut down 30 min-
utes after starting. If any other indicator light is on
after starting, the engine will shut down in a few
seconds. Investigate any indicated problem.
9. Allow the engine to warm up at low idle speed for
several minutes before applying a load and/or
switching to high idle. Allow a longer warm up time
in cold weather.
COLD WEATHER STARTING
With a fully charged battery and the proper weight oil,
the engine should start satisfactorily even down to
about 0
o
F.
If the engine must be frequently started below 10
o
F, it
may be desirable to install the optional Ether Start kit
(K825-1). Installation and operating instructions are
included in the kit. Use ether starting only when
required, because excessive use shortens engine life.
OPERATION
B-8 B-8
COMMANDER 400
Return to Section TOC Return to Section TOC Return to Section TOC Return to Section TOC
Return to Master TOC Return to Master TOC Return to Master TOC Return to Master TOC