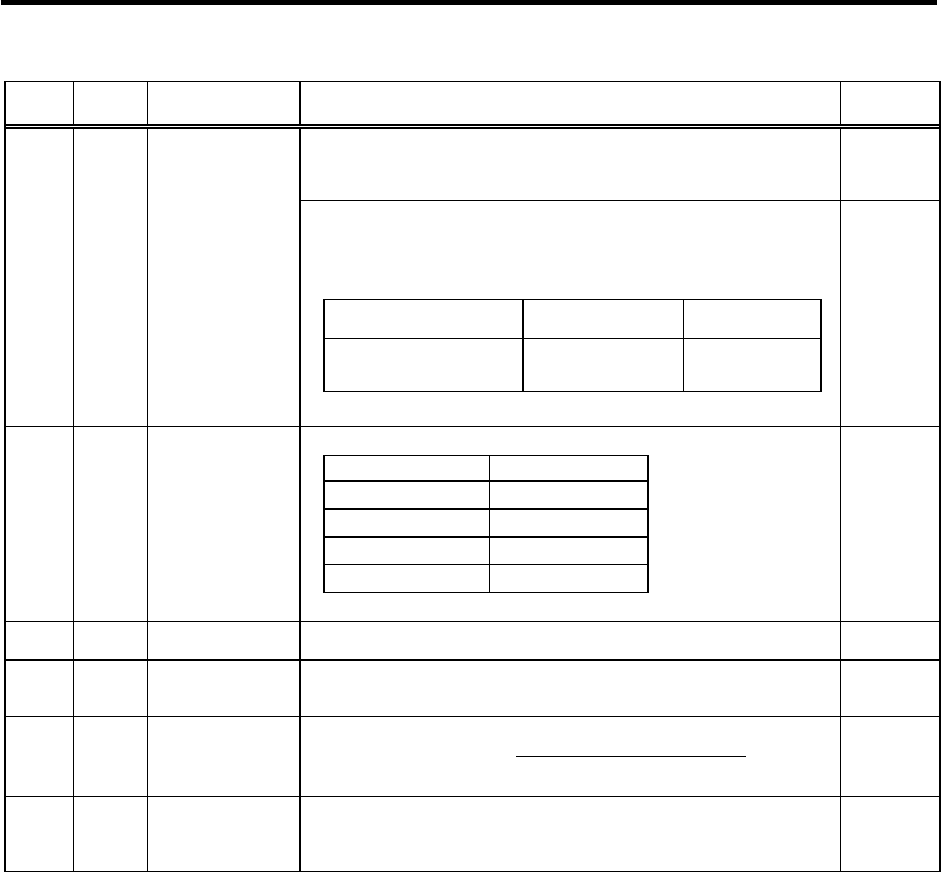
8. Setup
8 - 15
No. Abbrev. Parameter name Explanation
Setting
range (Unit)
In the case of the semi-closed loop control
Set the same value as SV020 (RNG2).
(Refer to the explanation of SV020.)
1 to 9999
(kp/rev)
In the case of the full-closed loop control
This is available for the relative position rectangular wave output
specification linear scale.
Set the number of pulses per ball screw pitch.
Detector model name Resolution SV019 setting
Relative position rectangular
wave output scale
Refer to detector
specification manual.
SV018 (PIT)(mm)/
Resolution (µm)
SV019 RNG1*
Position detector
resolution
1 to 9999
(kp/PIT)
Set the number of pulses per one revolution of the motor side detector.
Motor type SV020 setting
HF□□-A42 100
HF□□-A47 100
HF□□-A48 260
HF□□-A51 1000
SV020 RNG2*
Speed detector
resolution
1 to 9999
(kp/rev)
SV021 OLT
Overload detection
time constant
Set the detection time constant of Overload 1 (Alarm 50).
Set to "60" as a standard. (For machine tool builder adjustment.)
1 to 999
(s)
SV022 OLL
Overload detection
level
Set the current detection level of Overload 1 (Alarm 50) in respect to the
stall (rated) current.
Set to "150" as a standard. (For machine tool builder adjustment.)
110 to 500
(Stall
current %)
Set the excessive error detection width when servo ON.
Rapid traverse rate (mm/min) <Standard
setting value>
OD1=OD2=
60×PGN1
/2 (mm)
SV023 OD1
Excessive error
detection width
during servo ON
When "0" is set, the excessive error detection will not be performed.
0 to 32767
(mm)
SV024 INP
In-position
detection width
Set the in-position detection width.
Set the accuracy required for the machine.
The lower the setting is, the higher the positioning accuracy gets, however,
the cycle time (setting time) becomes longer. The standard setting is "50".
0 to 32767
(m)
Parameters with an asterisk * in the abbreviation, such as PC1*, are validated with the NC power is turned ON again.