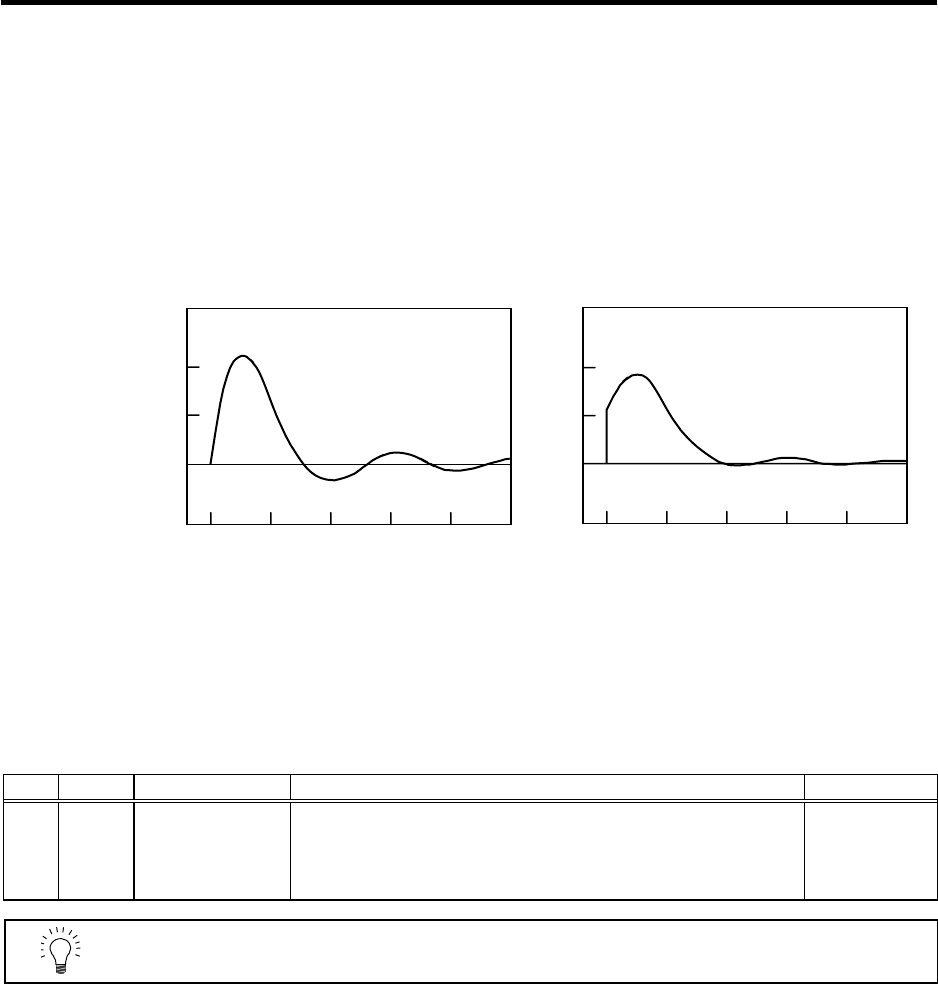
9. Adjustment
9 - 27
(2) Acceleration feed forward
Vibration may occur at 10 to 20 Hz during acceleration/deceleration when a short time constant of
30 ms or less is applied, and a position loop gain (PGN1) higher than the general standard value or
SHG control is used. This is because the torque is insufficient when starting or when starting
deceleration, and can be resolved by setting the acceleration feed forward gain (SV015 (FFC)).
This is also effective in reducing the peak current (torque).
While measuring the current command waveform, increase FFC by 50 to 100 at a time and set the
value where vibration does not occur.
100
8060 40
200
Ti
me (ms
)
200
100
100
806040
20 0
0
200
Current
command
(%)
100
0
Time (ms
)
No FFC setting With FFC setting
Acceleration feed forward gain means that the speed loop gain during acceleration/deceleration is
raised equivalently. Thus, the torque (current command) required during acceleration/deceleration
starts sooner. The synchronization precision will improve if the FFC of the delayed side axis is
raised between axes for which high-precision synchronous control (such as synchronous tapping
control and superimposition control).
No. Abbrev. Parameter name Explanation Setting range
SV015 FFC Acceleration rate
feed forward gain
When a relative error in the synchronous control is large, apply this
parameter to the axis that is delaying. The standard setting value is “0”.
For the SHG control, set to "100".
To adjust a relative error in acceleration/deceleration, increase the value
by 50 to 100 at a time.
0 to 999
(%)
POINT
Overshooting occurs easily when a value above the standard value is set during
SHG control.