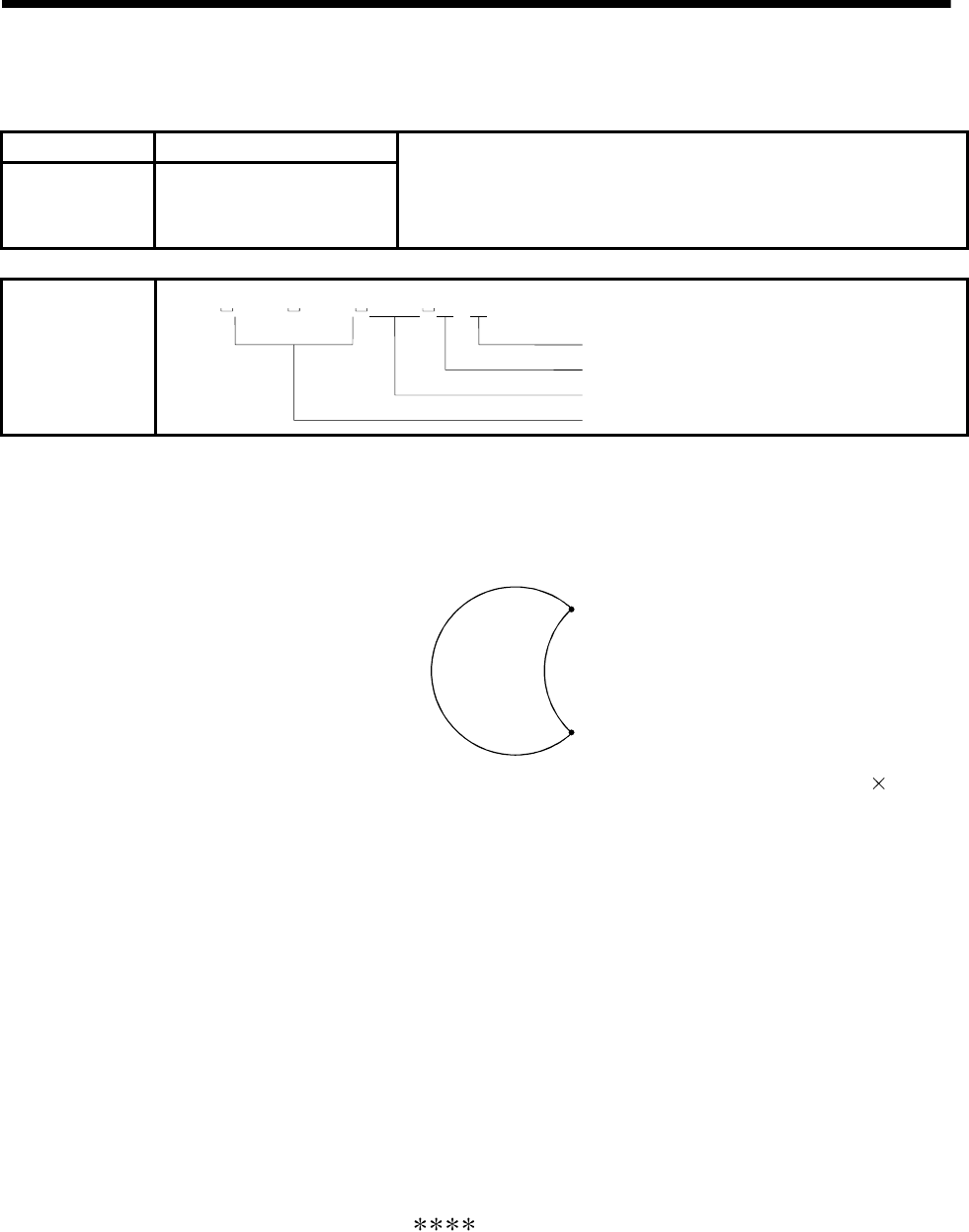
6 - 64
6 MOTION PROGRAMS FOR POSITIONING CONTROL
6.13.6 G03 Circular interpolation CCW (Radius-specified)
Code G03
Function
Circular interpolation (CCW)
Radius specified circular
interpolation
The axes travel from the current position (start point) to the specified
coordinate position (end point) with a circular arc of the specified radius
(CCW).
The travel speed is the specified feed rate.
Format
0
Feed rate
Feed rate command
3XxGYyRr
Circular arc radius
End point X, Y coordinates
;Ff
[Explanation]
(1) A circular arc of more than 180° is drawn at a negative circular arc radius (R)
value, or a circular arc of 180° or less is drawn at a positive R value.
Always use an incremental value to command the R value.
Radius value Positive
End point
Radius value Negative
Start point
An error will occur if "the distance between start and end points" - radius
2 >
"circular arc error".
(2) If a complete round command (the start point is the same as the end point) is
specified in R-specified circular interpolation, an error (error code : 108) will occur
and no operation is performed. Therefore, specify the circular arc central
coordinates for the complete round command.
(3) When this command is executed continuously, the acceleration or deceleration is
not made at the start or end point of a block because the status is not the exact
stop check mode.
(4) When the circular arc central coordinates and radius are specified simultaneously
for G03 (CCW), the radius-specified circular interpolation has priority.
(5) The positioning data can be set by direct setting (numerical value) or indirect
setting (variable : #
).