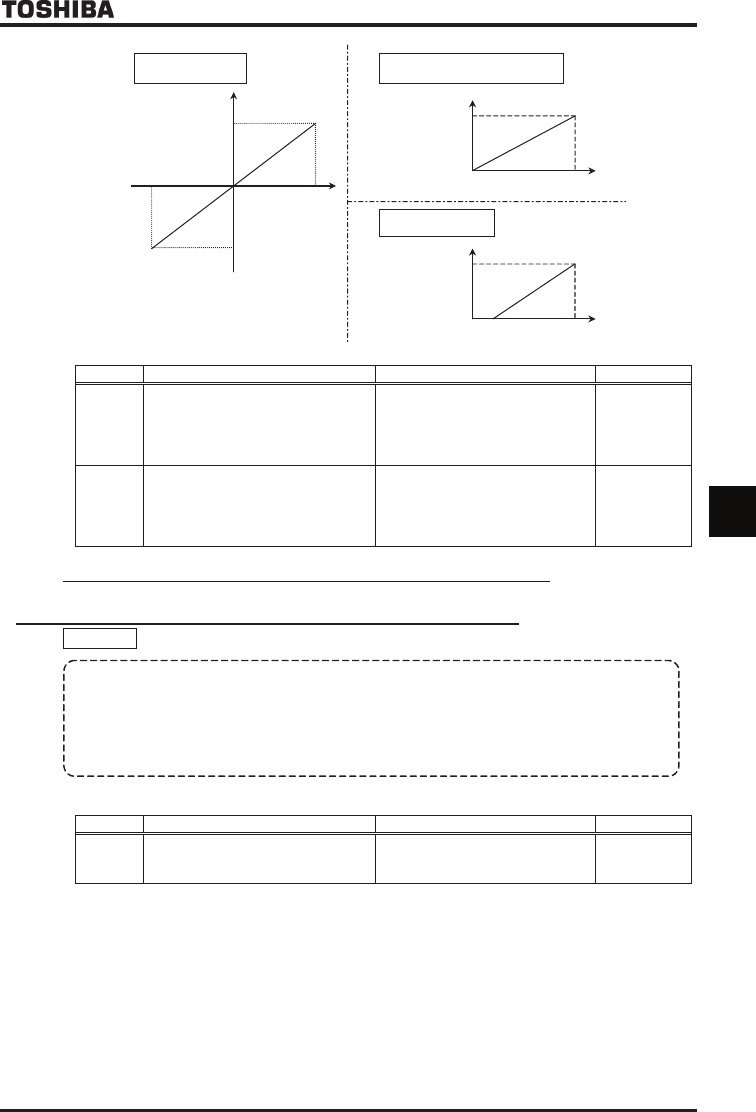
E6581301
F-47
6
0
4mA 20mA
0V
-100%
+10V
-10V
0%
100%
+100%
100%
Torque produced
by motor
Torque produced
by motor
Torque produced
by motor
0
0V
10V
RX-CCA
VI/II-CCA
RR/S4 -CCA, VI/II-CCA
[Parameter setting]
Title Function Adjustment range Default setting
H Power running torque limit 1 selection
:VI/II (voltage/current input)
:RR/S4 (potentiometer/voltage
input)
:RX (voltage input)
:H
H
Regenerative braking torque limit 1
selection
:VI/II (voltage/current input)
:RR/S4 (potentiometer/voltage
input)
:RX (voltage input)
:H
In torque control mode, the values set with these parameters limit torque command values.
6.25.2 Torque limit mode selection at acceleration/deceleration
H
HH
H
: Acceleration/deceleration operation after torque limit
•
••
• Function
Using this function in combination with the mechanical brake of the lifting gear (such as a crane or hoist)
makes it possible to minimize the delay before the brake starts working, and thus prevents the load from
falling because of a decrease in torque.
Moreover, it improves the motor’s response during inching operation and keeps the load from sliding down.
[Parameter setting]
Title Function Adjustment range Default setting
H
Acceleration/deceleration operation after
torque limit
: In sync with
acceleration/deceleration
: In sync with min. time
(1) H= (In sync with acceleration/deceleration)
The increase in operation frequency is inhibited by the activation of the torque limit function. In this control mode,
therefore, the actual speed is always kept in sync with the operation frequency. The operation frequency restarts
to increase when torque decreases as a result of the release of the mechanical brake, so the time required for the
specified speed to be reached is the sum of the delay in operation of the mechanical brake and the acceleration
time.