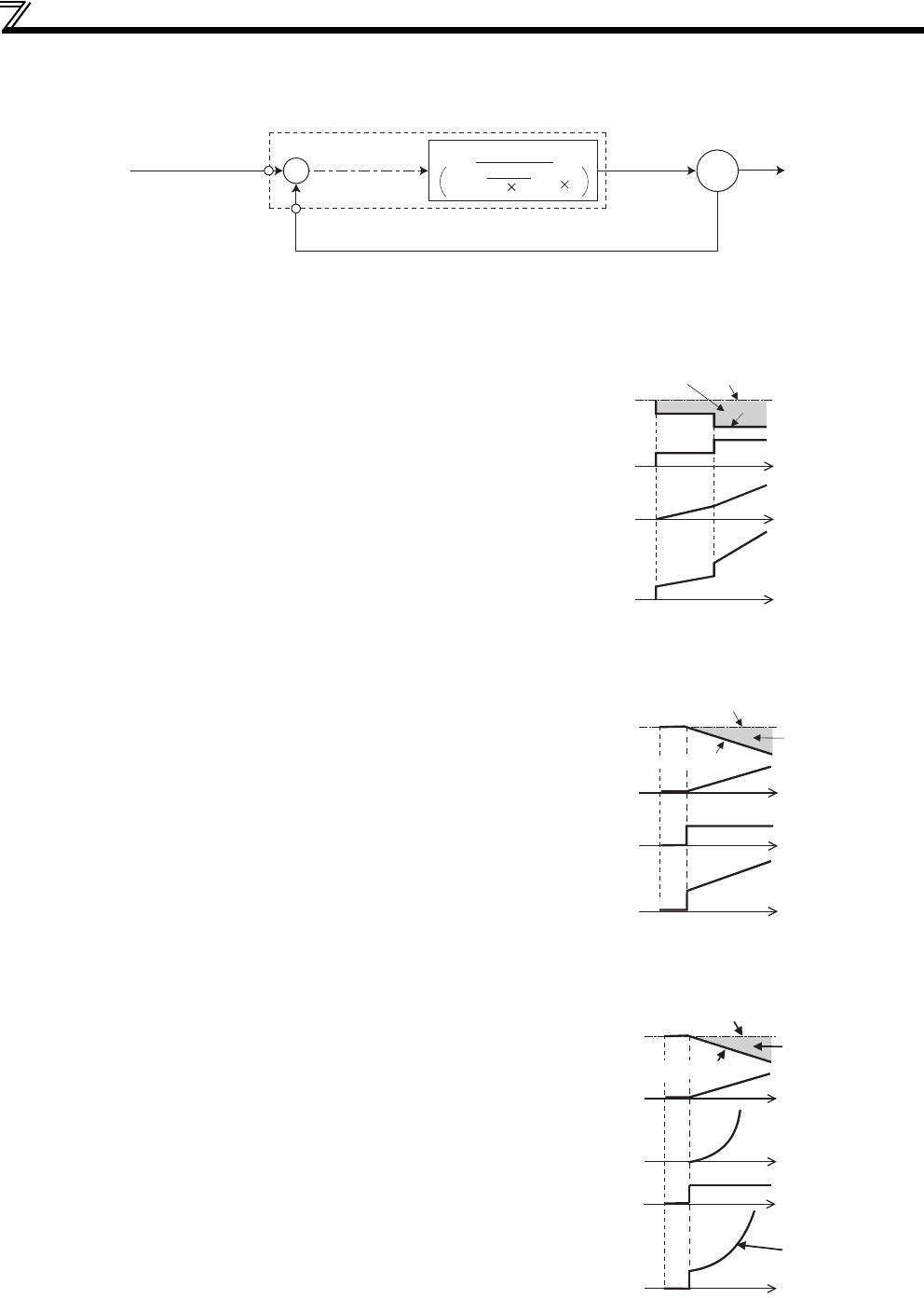
236
Special operation and speed control
(1) PID control basic configuration
Pr.128 = "20, 21" (measured value input)
(2) PID action overview
1) PI action
2) PD action
3) PID action
A combination of proportional control action (P) and integral control
action (I) for providing a manipulated variable in response to deviation
and changes with time.
[Operation example for stepped changes of measured value]
(Note) PI action is the sum of P and I actions.
A combination of proportional control action (P) and differential control
action (D) for providing a manipulated variable in response to deviation
speed to improve the transient characteristic.
[Operation example for proportional changes of measured value]
(Note) PD action is the sum of P and D actions.
The PI action and PD action are combined to utilize the advantages of
both actions for control.
(Note) PID action is the sum of P, I and D actions.
+
-
M
Pr.133
or terminal 2
Set point
Drive unit circuit
Motor
Feedback signal (measured value)
Terminal 4
Kp: Proportionality constant Ti: Integral time S: Operator Td: Differential time
Manipulated
variable
0 to 5VDC
(0 to 10VDC)
4 to 20mADC (0 to 5V, 0 to 10V)
PID operation
Ti S
1
Kp 1+ +Td S
Deviation
Set point
Measured value
Time
Time
Time
PI action
I action
P action
Deviation
Set point
Time
Time
Time
PD action
D action
P action
Measured value
Deviation
Set point
PID action
D action
P action
I action
y=at +bt+c
2
Time
Time
Time
Time
Measured value