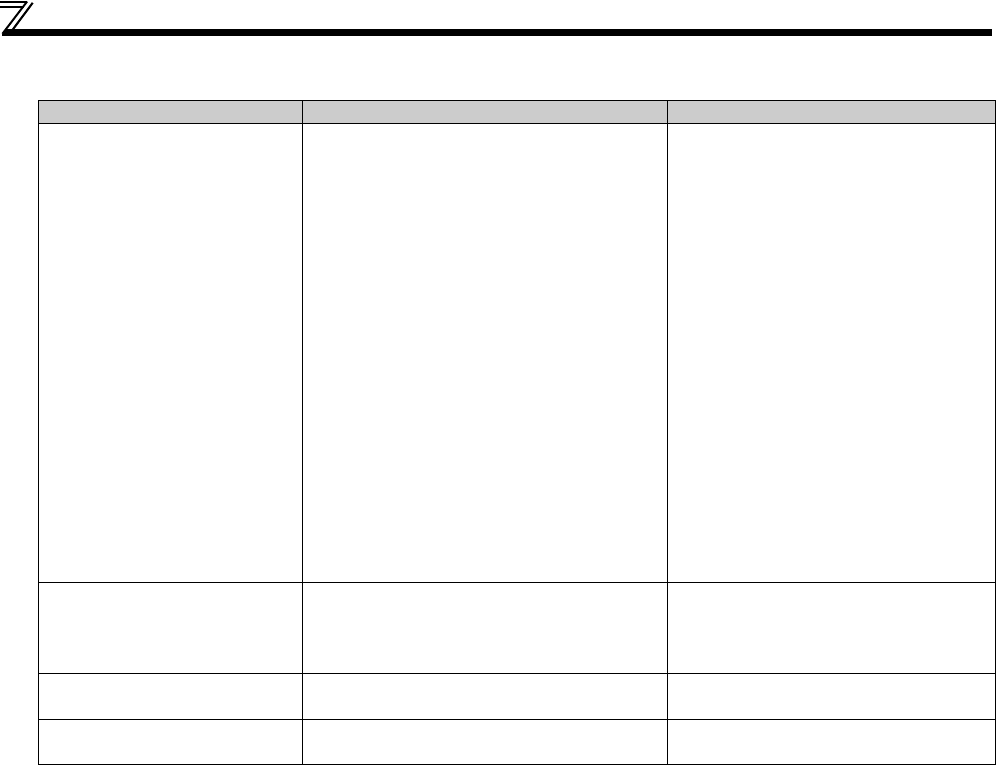
94
Position control
(7) Troubleshooting (for position control)
Condition Cause Countermeasure
The motor does not rotate.
(1) The phase sequence of motor wiring is
incorrect.
(2) The setting of Pr.800 is not appropriate.
(3) Any of the following signals are not input:
servo-ON signal (SON), pre-excitation signal
(LX), point table selection signal (RH, RM, or
RL), and start signal (STF or STR).
(4) Any of the following signals are input:
position control sudden stop signal (X87)
(normally closed), forward stroke end signal
(LSP) (normally closed), reverse stroke end
signal (LSN) (normally closed), and PU stop
signal.
(5) The target position setting in Pr.465 to Pr.485
is incorrect.
(6) The number of droop pulses [after the
electronic gear] has exceeded the Pr.427
Excessive level error setting.
(1) Check the wiring.
(2) Check the Pr.800 setting.
(3) Check if the signals are properly input.
(4) Check if the signals are properly input.
(5) Check the target position setting in
Pr.465 to Pr.485.
(6) Check the Pr.427 Excessive level error
setting.
The position is unfavorably shifted.
(1) The point table selection signal (RH, RM, or
RL) is not input.
(2) The electronic gear settings in Pr.420 and
Pr.421 are incorrect.
(1) Check the wiring.
(2) Check the electronic gear settings by
Pr.420 and Pr.421.
Hunting occurs in the motor or the
machine.
(1) Position loop gain is too high.
(2) Speed loop gain is too high.
(1) Set Pr.422 lower.
(2) Set Pr.820 lower and Pr.821 higher.
Machine movement is unstable.
(1) Acceleration/deceleration time settings are
affecting adversely.
(1) Set the acceleration/deceleration time
(Pr.578 to Pr.591) lower.