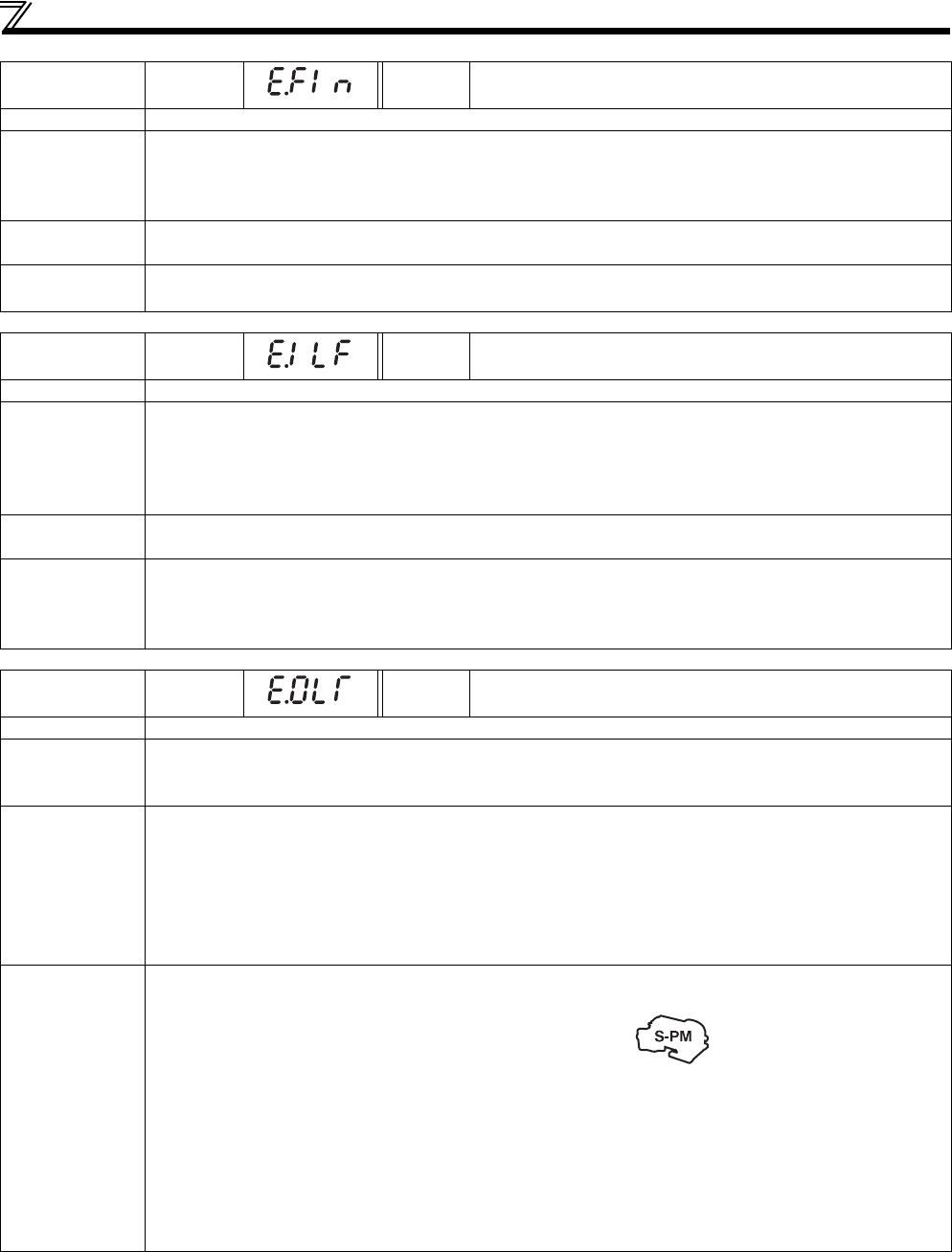
274
Causes and corrective actions
Operation panel
indication
E.FIN
FR-PU07 H/Sink O/Temp
Name
Heatsink overheat
Description
If the heatsink overheats, the temperature sensor is actuated and the drive unit trips.
The FIN signal can be output when the temperature becomes approximately 85% of the heatsink overheat protection
operation temperature. For the terminal used for the FIN signal output, assign the function by setting "26 (positive
logic) or 126 (negative logic)" in any of Pr.190 to Pr.192 (output terminal function selection). (Refer to page 144)
Check point
Check for too high surrounding air temperature.
Check for heatsink clogging.
Corrective
action
Set the surrounding air temperature to within the specifications.
Clean the heatsink.
Operation panel
indication
E.ILF
FR-PU07 Input phase loss
Name
Input phase loss
Description
Drive unit trips when function valid setting (=1) is selected in Pr.872 Input phase loss protection selection and one phase
of the three phase power input is lost. (Refer to page 166)
It may be available if phase-to-phase voltage of the three-phase power input becomes largely unbalanced.
When the setting of Pr.872 Input phase loss protection selection is the initial value (Pr.872 = "0"), this warning does not
occur.
Check point
Check for a break in the cable for the three-phase power supply input.
Check that phase-to-phase voltage of the three-phase power input is not largely unbalanced.
Corrective
action
Wire the cables properly.
Repair a break portion in the cable.
Check the Pr.872 Input phase loss protection selection setting.
Set Pr.872 = "0" (without input phase loss protection) when three-phase input voltage is largely unbalanced.
Operation panel
indication
E.OLT
FR-PU07 Stll Prev STP
Name
Stop by the torque limit
Description
If the rotation speed drops to 18r/min or lower due to the torque limit operation and stays there for 3s, the fault
indication (E.OLT) appears, and the drive unit outputs are shut off. OL appears during the torque limit operation.
E.OLT may not occur if torque limit (OL) is activated during output phase loss.
Check point
Any of the acceleration time set by Pr.7 Acceleration time, deceleration time set by Pr.8 Deceleration time, and
positioning acceleration/deceleration time set by Pr.578 to Pr.591 is too short.
Check for torque shortage in a low-speed range.
Check if the acceleration/deceleration time in a low-speed range is too short.
Check that the load is not too heavy.
Are there any failure in peripheral devices?
Check that the Pr.22 Torque limit level is appropriate
Corrective
action
Set a larger value in Pr.7 Acceleration time, Pr.8 Deceleration time, and positioning acceleration/deceleration time set in
Pr.578 to Pr.591. (Refer to page 125)
Set a larger value in Pr.785 PM control torque boost. (Refer to page 114)
Set longer times in Pr.791 Acceleration time in low-speed range and Pr.792 Deceleration time in low-speed range. (Refer to
page 125)
Reduce the load weight.
Set the torque limit operation current in
Pr.22 Torque limit level
. (The initial value differs according to the drive unit
capacity and the motor being used.) Acceleration/deceleration time may change. Increase the torque limit operation
level with
Pr.22 Torque limit level
, or disable the torque limit operation with
Pr.156 Torque limit selection
. (Operation at
OL occurrence can be selected using Pr.156.)
Check the connection of the PM motor.