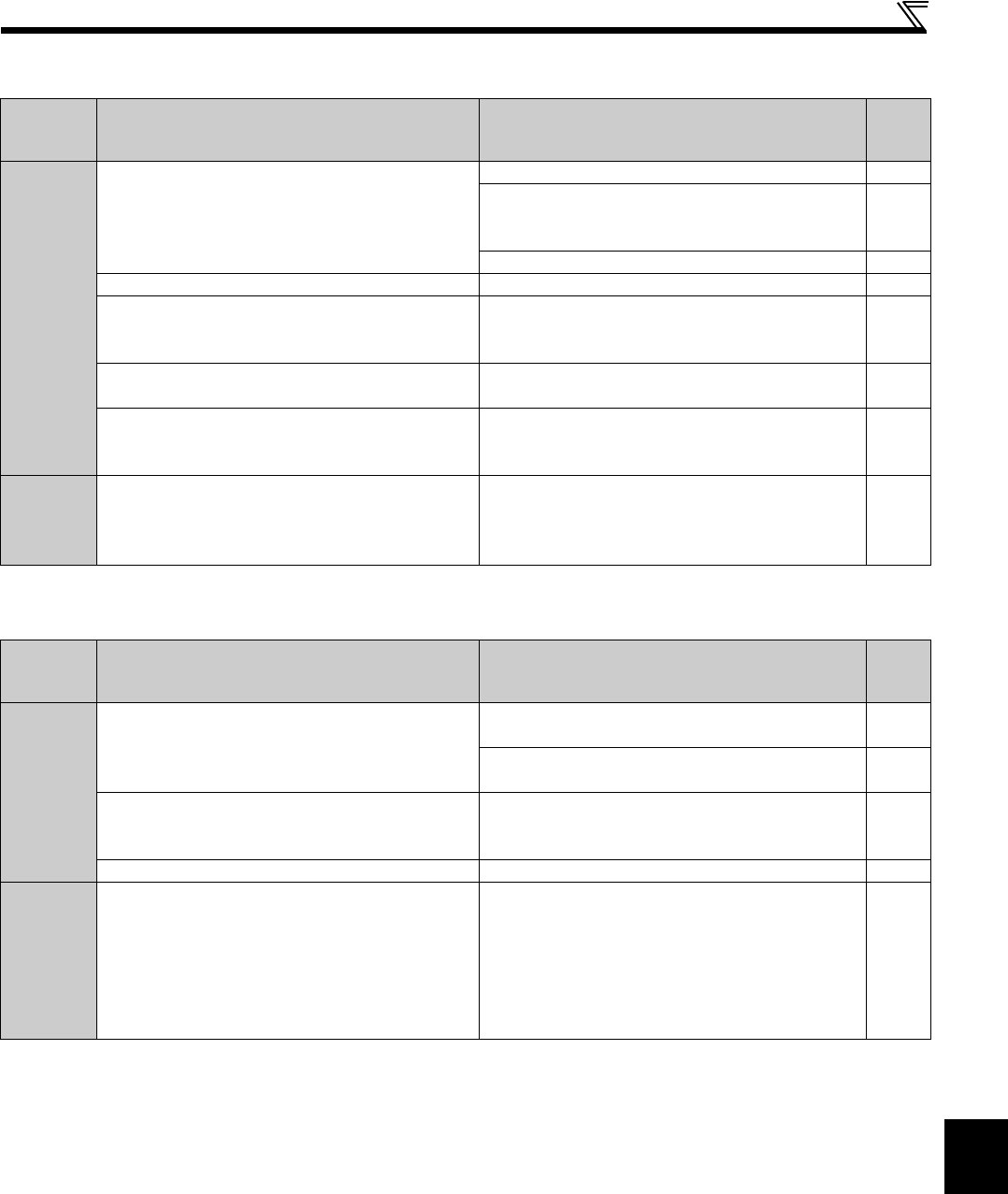
283
Check first when you have a trouble
5
TROUBLESHOOTING
5.5.6 Acceleration/deceleration is not smooth
5.5.7 Speed varies during operation
Check
Points
Possible Cause Countermeasures
Refer
to
page
Parameter
Setting
Torque limit function is activated due to a heavy load.
Reduce the load weight.
Set Pr.22 Torque limit level higher according to the load.
(Setting Pr.22 too large may result in frequent
overcurrent trip (E.OC).)
111
Check the capacities of the drive unit and the motor.
Acceleration/deceleration time is too short. Increase acceleration/deceleration time. 125
Regeneration avoidance operation is performed
If the speed becomes unstable during regeneration
avoidance operation, decrease the setting of Pr.886
Regeneration avoidance voltage gain.
242
Pr.791 and Pr.792 (Acceleration/deceleration time in low-
speed range) are set.
Check the Pr.791 and Pr.792 (Acceleration/deceleration time
in low-speed range) settings.
125
When any mechanical looseness or load fluctuation
exists, the motor resistance calculated by the drive unit
is inaccurate.
Set the wiring resistance value in Pr.658 Wiring resistance. 87
Others
Mechanical looseness or load fluctuation
Adjust machine/equipment so that there is no
mechanical looseness. Eliminate the load fluctuation.
Use Pr.156 Torque limit selection to disable the torque
limit.
111
Check
Points
Possible Cause Countermeasures
Refer
to
page
Input
Signal
The speed setting signal is affected by EMI.
Set filter to the analog input terminal using Pr.74 Input
filter time constant.
172
Take countermeasures against EMI, such as using
shielded wires for input signal lines.
36
Malfunction is occurring due to the undesirable current
generated when the transistor output unit is connected.
Use terminal PC (terminal SD when source logic) as a
common terminal to prevent a malfunction caused by
undesirable current.
21
Multi-speed command signal is chattering. Take countermeasures to suppress chattering.
Parameter
Setting
Hunting occurs by the generated vibration, for example,
when structural rigidity at load side is insufficient.
Disable automatic control functions, such as
regeneration avoidance function and torque limit
operation.
During the PID control, set smaller values to Pr.129 PID
proportional band and Pr.130 PID integral time.
Lower the control gain, and adjust to increase the
stability.