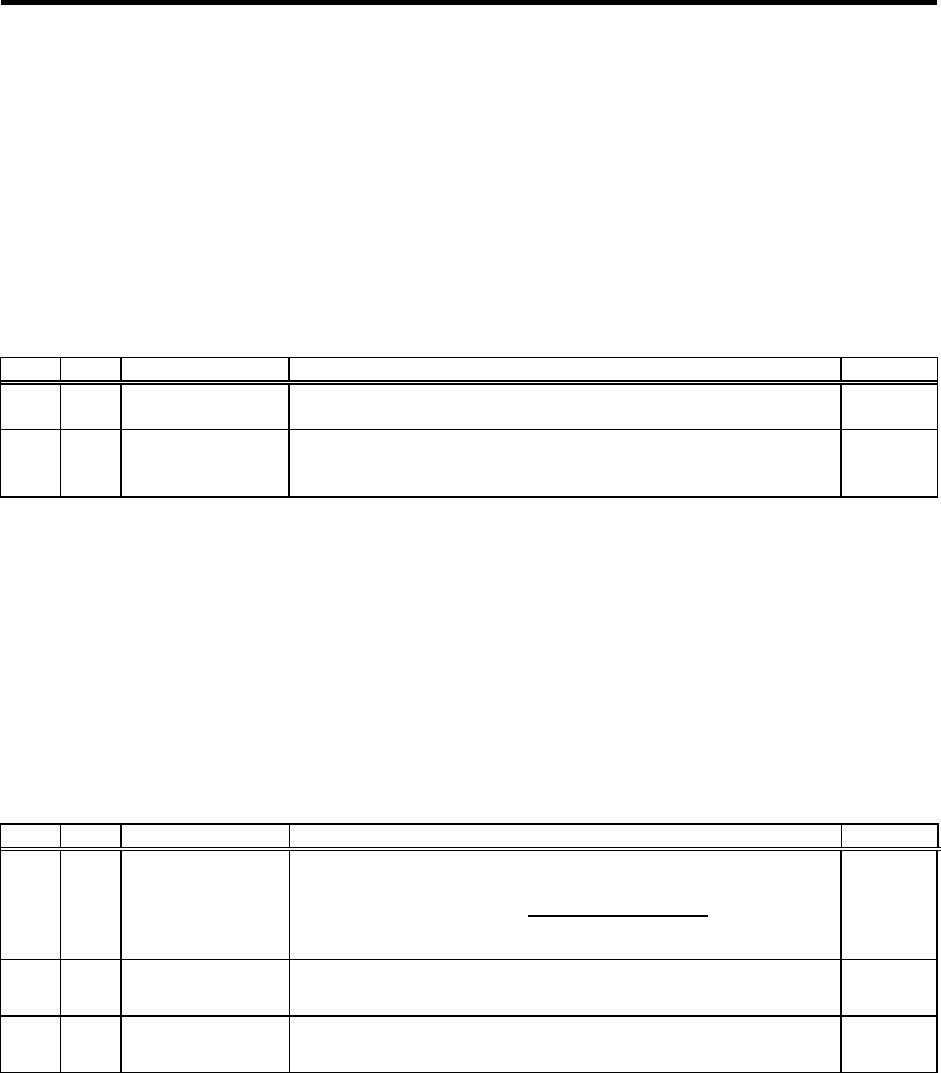
4. Servo Adjustment
4 - 43
4-6 Protective functions
4-6-1 Overload detection
The servo drive unit is equipped with an electronic thermal that protects the servomotor and servo drive
unit from overload conditions. The overload 1 alarm (alarm 50) is detected if an overload condition
occurs, and the overload 2 alarm (alarm 51) is detected if 95% or more of the maximum current is
commanded continuously for 1 second or longer due to a machine collision, etc. The parameters
shown below are for machine tool builder adjustment purposes only, and should be kept at their
standard settings (SV021=60, SV022=150).
For details concerning the overload protection characteristics, refer to the MDS-C1 Series Specifications
Manual (BNP-C3040).
No. Abbrev. Parameter name Explanation Setting range
SV021 OLT
Overload detection
time constant
Set the detection time constant of Overload 1 (Alarm 50).
Set to "60" as a standard. (For machine tool builder adjustment.)
1 to 999
(s)
SV022 OLL
Overload detection
level
Set the current detection level of Overload 1 (Alarm 50) in respect to the
stall (rated) current.
Set to "150" as a standard. (For machine tool builder adjustment.)
110 to 500
(Stall [rated]
current %)
4-6-2 Excessive error detection
An excessive error (alarms 52, 53, 54) is detected when the difference between the servo's
commanded position and the FB position exceeds the value set by parameter. Separate excessive
error detection width can be set for servo ON (SV023) and servo OFF (SV026) statuses. When a wider
excessive error detection width than that used for standard control is required in stopper control, etc.,
the detection width setting can be changed to the SV053 setting value by NC command.
Follow-up control (NC commanded position tracks servo FB position) is used during emergency stop
and during a servo OFF command, and so there is no excessive error detection at those times,
although the follow-up control during a servo OFF status can be disabled by an NC system parameter
setting.
No. Abbrev. Parameter name Explanation Setting range
Set the excessive error detection width when servo ON.
Rapid traverse rate
(mm/min)
<Standard
setting value>
OD1=OD2=
60
× PGN1
÷ 2 (mm)
SV023 OD1
Excessive error
detection width
during servo ON
When "0" is set, the excessive error detection will not be performed.
0 to 32767
(mm)
SV026 OD2
Excessive error
detection width
during servo OFF
Set the excessive error detection width when servo ON.
For the standard setting, refer to the explanation of SV023 (OD1).
When "0" is set, the excessive error detection will not be performed.
0 to 32767
(mm)
SV053 OD3
Excessive error
detection width in
special control
Set the excessive error detection width when servo ON in a special control
(initial absolute position setting, stopper control, etc.).
If "0" is set, excessive error detection won’t be performed.
0 to 32767
(mm)