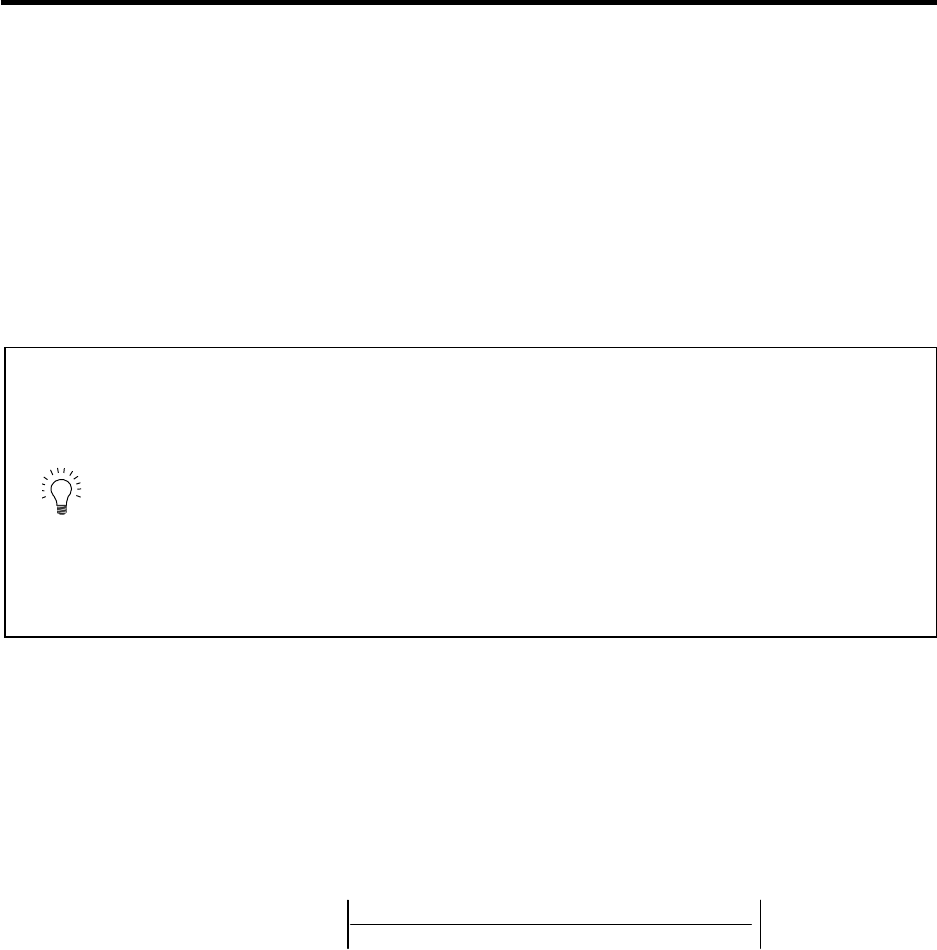
4. Servo Adjustment
4 - 45
(2) Collision detection method 2
When the current command reaches the motor's maximum current, the motor will decelerate and
stop at a torque 80% (standard value) of the motor's maximum torque. After decelerating to a stop,
alarm 5A will occur, and the system will stop. If the acceleration/deceleration time constant is short
and incorrect detections easily occur during normal operation, lengthen the acceleration/
deceleration time constant and adjust so that the current is not saturated (does not reach the
maximum current) during acceleration.
If the acceleration/deceleration time constant cannot be lengthened, set parameter SV035/bitF
(SSF4.c12n) to 1 to ignore collision detection method 2.
POINT
1. Always validate SHG control when using the collision detection function, or
when carrying out SV059 setting value operation.
2. Provide an allowance in the detection level setting to prevent incorrect
detections.
3. All collision detection functions will be disabled when SV60 is set to 0.
4. Collision detection method 2 will function if a value other than 0 is set in
SV060. Note that the detection can be ignored by setting the parameter
(SV035/bitB).
5. The torque estimated gain (SV059) must be readjusted when there are
changes in the detector resolution following the detector replacement, or in
the detector loop gain (PGN) or position control system. (closed loop control
and semi-closed loop has been changed).
<Setting and adjustment methods>
[1] Confirm that SHG control is active. Collision detection function is valid only during SHG control.
[2] Set the axis unbalanced torque to the torque offset (SV032: TOF). (Refer to "4-3-5 (1)
Unbalance torque and frictional torque" for details on measuring the unbalance torque.)
[3] Measure the frictional torque and set in the frictional torque (SV045: TRUB). Carry out
reciprocation operation (approx. F1000) with the axis to be adjusted, and measure the load
current % when the axis is fed at the constant speed on the NC SERVO MONITOR screen.
This frictional torque is expressed with the following expression.
[4] Set SV035: SSF4.clt (bitF) to 1 for the axis being adjusted, and move in both directions with
JOG, etc., at the rapid traverse rate. When the MPOS display on the NC SERVO MONITOR
screen has stabilized, set that value for the torque estimated gain (SV059: TCNV). Return
SV035: SSF4.clt (bitF) to 0.
[5] If the acceleration/deceleration time is short, and the current is limited, set SV035: SSF4.c12n
(bitB) to 1 to invalidate collision detection method 2.
[6] Adjust the collision detection level (SV060: TLMT). First set 100. If operation at the rapid
traverse rate results in an alarm, increase the setting value by approx. 20. If an alarm does not
occur, lower the setting value by approx. 10. When SV035: SSF4.clet (bitA) is set to 1, the
estimated disturbance torque peak value for the latest two seconds will appear at MPOS. This
value can be used as reference. Set the final setting value to a value approx. 1.5-fold the limit
value at which an alarm does not occur.
[7] Divide the maximum cutting load with the value set for the collision detection level (SV060:
TLMT). (Round up the decimal) Set this value in SV035: SSF4.clG1 (bitC-E).
2
(+ feed load current %) - (- feed load current %)
Frictional tor
q
ue
(
%
)
=